Pending
Industrial-Output Signal Conditioners Simplify the Design of PLCs and Industrial Control/Automation Systems
Maxim has introduced the MAX15500/MAX15501 industrial analog-output signal conditioners. These devices offer the industrial market a unique combination of higher functionality, greater integration, and smaller total solution size than competitive devices. They feature unprecedented integration: a programmable voltage-output amplifier and a current-output amplifier; ±10V and 4-20mA outputs operating directly from a 24V field supply; ±35V circuit protection; extensive error reporting capability; and daisy-chain flexibility.
The MAX15500/MAX15501 save board space and design time in 4-20mA and/or bipolar/unipolar voltage-output applications. They are ideal for PLC (programmable logic controller) analog outputs, distributed I/O, embedded systems, and industrial control and automation. Their high integration adds flexibility for designs. Use a single device for channel-isolated applications or multiple devices for group-isolated applications. The MAX15500/MAX15501 simplify the design of PLC modules. Typical competitive signal conditioners need precision-matched resistors to track voltages well over temperature. The MAX15500/MAX15501s' integrated voltage amplifier and voltage-to-current converter eliminate the need for those additional resistors, thus saving valuable board space. Only the current gain-setting resistor is external to the device. They offer extensive fault detection, including open-circuit load in current mode, short-circuit load in voltage mode, overtemperature, and supply brownout. Both intermittent and permanent load faults can be detected. If a fault occurs, the open-drain fault-interrupt pin will be pulled low. These are the only devices on the market with all these integrated features. The status of the fault bits is available through the SPI(TM) interface.
The MAX15500/MAX15501 analog output conditioners give a +5% and +20% over range, providing a programmable current up to ±24mA or voltage up to ±12V proportional to a control-voltage signal, as required by PLC manufacturers. The control voltage is typically supplied by an external DAC with an output voltage range of 0 to 4.096V for the MAX15500, and 0 to 2.5V for the MAX15501.
The output current and voltage are selectable as either unipolar or bipolar. Additionally, a HART signal may be added to the input signal.
Many industrial-control systems require error detection and error handling. Typical competitive devices use 3x the number of interrupt flags for error detection, thus requiring more pins and potentially more optoisolators. None of these fault pins are latched, so the competition needs more microcontroller interrupts to detect intermittent errors. In addition, competitive devices monitor fewer sources of error, and none of them offer power-supply monitoring.
In striking contrast, the MAX15500/MAX15501 have extensive error-handling and the best error-reporting capabilities in their class of products. Instead of using separate interrupt pins, the MAX15500/MAX15501 report the status of short-circuit, open-circuit, brownout, and overtemperature conditions through an SPI interface and an additional open-drain interrupt output. This fault detection scheme reduces the I/O pin count and software loading required by the host processor. For error tracking and troubleshooting systems, an error register stores the error source. Uniquely, the MAX15500/MAX15501 include an analog output to monitor the load. These are the only signal conditioners to do PSU monitoring.
Designers can now operate their output conditioners directly from a ±24V field power supply, said Jeremy Tole, Maxim's Director of Business Development for Data Converters. Running directly off the ±24V supply is a marked improvement over competitive solutions which require the use of an external voltage regulator. Additionally, the MAX15500/MAX15501 have a standard field supply of ±24V, ±20%. Competitive devices can only operate at a maximum supply voltage of ±22V. Therefore, the competition needs an external regulator to implement their solution for ±24V.
With their higher ±24V supply voltage, the MAX15500/MAX15501 can handle a typical load of 750ohms in current mode. With ±32.5V supplies, this increases to 1000ohms. Designers can be confident that their device outputs are protected against a ±35V field power supply. This is a unique feature of these devices, added Tole. This voltage protection will save money and board space since the additional protection circuitry typically required in other solutions is not necessary.
Additionally, the MAX15500/MAX15501 outputs, power-supply inputs, and sense inputs are protected against overcurrent conditions, a short to ground, or supply voltages up to ±35V.
The MAX15500/MAX15501 are programmed through a 3-wire SPI-/QSPI(TM)-/MICROWIRE(TM)-/DSP-compatible serial interface with daisy-chain capability. This is the preferred interface because it saves board space and reduces the complexity of optically-isolated and transformer-isolated applications. A device-ready logic output and two device-select inputs facilitate a daisy-chain arrangement for multiple device applications. A chain of MAX15500/MAX15501 devices can be terminated with any standard SPI-compatible single device. The MAX15500/MAX15501 portion of the chain continues to display timing parameters comparable to a single device.
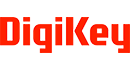