Automotive high power comes in small packages
The automotive industry is no stranger to innovation, writes Steve Sheard, ON Semiconductor. This introduces drivers to new features and levels of comfort, but require innovation in the fundamental structure and make up of a car’s electrical and power systems.
With the automotive industry increasingly buoyant and new vehicle sales strong in many key regions, now is the time for looking to the key technologies that will underpin future generations of cars. The nature of the global recession led to a slow-down in some areas of research and development for new cars and technologies. With demand once again growing in the traditional markets of the US and Europe, alongside giant markets in the far-east, it is clear that the drive has again returned to the automotive industry.
Presently, demand for low power consumption and energy saving electronic products is increasing as industry responds to global trends and government legislation, encouraging efficiency and environment concern. Simultaneously, the development and rising popularity of alternative fuel source vehicles is creating demand in entirely new areas.
Power MOSFETs play a crucial role in all modern vehicles. From the systems managing and monitoring oil pressure and anti-lock braking systems to power steering, airbags and climate control, the requirement for high-quality, robust transistors, capable of handling the power levels in these applications, is substantial.
Figure 1: The key areas where a modern car will make use of power MOSFETs
However the specialised nature and requirements of automotive technology cannot always be easily solved with off the shelf products. Instead, manufacturers need to respond with effective power MOSFETs and other semiconductors which can meet these demanding and specialist tasks.
The car of the future - today
In the automotive industry the rule has normally been to aim for more. More power, more comfort, greater efficiency, more of pretty much everything - apart from weight. Better performance and higher efficiency are now almost wholly dependent on shedding weight elsewhere in the structure, frame, electrical systems and wiring. Long term increases in the cost of fuel ensure that this is a trend that will continue, necessitating ever smaller, more compact and integrated components.
This desire for less weight, however, is contrasted against the demand for vehicles with an exponential improvement and enhancement of media, comfort and safety features. In short, both manufactures and drivers are seeking more from a car, while expecting it to weigh less and cost less to run.
Even just over a decade ago, cars were substantially less advanced vehicles. The average family saloon may have been fitted with a basic stereo or CD player and electric windows, but features beyond this were commonly the preserve of premium and luxury vehicles. Now it is common for even the most affordable cars to offer Bluetooth connectivity for phones and media players.
Safety has, for a long time, been a key concern to both drivers and manufacturers. Increased quality of build and design have ensured ever better standards of safety. However the most recent advances have been related to advanced driver assistance systems (ADAS) and technologies. Applications such as lane departure warning (LDW) and forward collision warning (FCW) demand forward facing cameras, sensors and radar in order to effectively detect hazards. In turn, this places even greater expectations on the electric systems of a car, and more demand for power if greater operating efficiencies are not gained.
It is not merely what is inside, or underneath, a car that has seen an increase in complexity. The car itself has evolved. With the development and rise in popularity of hybrid, or fully electric vehicles, to address ever more stringent emissions legislation and regulation, all forms of semiconductors are in increased demand. The inverter systems within these fully or part electric cars, which convert DC battery voltage to AC, are dependent upon provision of power MOSFETs which can handle these high levels of power, heat and wear.
Multimedia motoring
Areas which have also seen huge growth in complexity and capability, within the automotive industry are those of in-car-entertainment, communication and information technology. This growing infotainment sector inevitably increases the complexity of the vehicle and its electrical system. Products and capabilities such as satellite navigation, Wi-Fi connectivity, 4G LTE and Bluetooth hands-free kits are increasing the digital domain for in-car use.
All of these features will inevitably place additional requirements and stresses on the car’s battery. DC/DC convertors for ensuring directional voltage current, plug-in chargers and battery monitoring equipment all require effective management of high power, and as such need power MOSFETs which are up to task.
MOSFETs for modern motors
Power MOSFETS have the potential to improve the overall efficiency of a car’s electrical systems by reducing losses of power caused by either conduction or switching. The type of requirements and expectations that a modern car places upon its electrical system necessitates components which promise reliability and quality at a price point which will not inflate the cost of the vehicle.
As a natural reaction to escalated fuel costs and the increasing affordability of high tech, lightweight construction materials it has become possible to make ever lighter vehicles, promising greater fuel efficiency and lower emissions. Yet the weight of these electrical systems have remained constant.
To address these concerns, packaging too has needed to move on. The latest power MOSFETs can be delivered in ever more compact packaging, making them capable of fitting into a smaller footprint and adding less weight to the vehicles.
However weight is not the sole consideration. The nature of automotive applications for power MOSFETs requires them to perform large-current drive control in highly adverse conditions, where motion, heat and wear can affect their performance and even cause them damage.
Figure 2: The trend for reduction in ratios of RDS(on)
ON Semiconductor has developed fine pitch trench and clip bonding technology to achieve lower RDS (on). Trench technology provides high cell densities as well as fine structures. Fine pitch trench technology is a proprietary solution that achieves lower on-resistance by reducing cell pitch on the gate compared to typical trench technologies.
Heat dissipation is another key issue, as the size of power MOSFET packages decreases, the internal temperature of these device increases exponentially due to difficulty in extracting excess heat. At higher currents, the on-resistance can increase further and more heat is generated. Heat impacts functionality, safety as well as reliability. ON Semiconductor developed the leading ATPAK package technology to increase possible heat dissipation.
Another issue, common in automotive environments, is that of electrostatic discharge (ESD). Due to the friction created by the moving parts throughout a car, and the dry air environment this common problem can cause a mechanical breakdown. The solution can be found in embedded protection diodes within the power MOSFET to help reduce and prevent ESD.
Key technology improvements such as these can be seen in addressing requirements for efficiency, power loss and heat dissipation. The increasingly small packages that contain the latest power MOSFETs will ensure that the applications demanding the most advanced forms of power distribution and management can be delivered by components in small, yet rugged form factors, which will allow future vehicles and the automotive industry to keep driving forward.
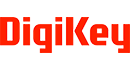