Addressing the challenges of e-bike design
Compared to traditional bicycle, e-bikes are significantly more expensive and consumers are looking for touchscreen interfaces and convenience, says Sven Hegner, chief engineer, Toshiba Electronics Europe
Since the 1990s, e-bikes have been growing in popularity with several sources predicting that close to half of all bicycles in the future will be fitted with a motor. China remains the primary market globally and in western Europe, Germany is leading the way, with over 650,000 e-bikes sold according to the bicycle industry federation (ZIV) in 2016. This was a significant portion of the 3m e-bikes sold outside China.
Features such as automatic gear changing, walk assist (where the e-bike can be pushed with minimal effort) and on-board navigation expand the offering. E-bikes are used for the daily commute. Range is clearly one parameter that influences purchase but, unlike with electric vehicles, an empty battery does not halt the journey. Batteries can also be easily charged at home or in the office, as required.
Design challenges
Beyond the complexities of the mechanical design, it is the motor, motor controller and battery system that deliver the fundamental design challenges for engineers. Motor control is a complex topic that requires experience to ensure excellent speed and torque control across a range of loads and speeds. The finite amount of energy available in the battery must be used as efficiently as possible. Larger batteries can provide more range, but this is at the cost of size and weight, leading to a larger proportion of energy being used simply to move the bicycle itself. As such, finding the correct compromise between range, efficient operation and battery capacity is the first step in the design process.
Figure 1: Toshiba’s Vector Engine allows complex calculations to be performed in hardware
Brushless DC (BLDC) motors offer significant benefits in both efficiency and reduced maintenance requirements compared to brushed DC motors. This is at the price of significantly more complicated electronic motor control since the commutation is no longer handled mechanically. Many methods are available but it is field oriented control (FOC) that overcomes the poor low speed accuracy of trapezoidal control and the high speed inefficiency of sinusoidal control. FOC does, however, brings its own set of challenges. It relies on a set of mathematical functions that transform stator current signals into the voltage-control signals that generate the necessary magnetic field to commutate the motor. Many solutions depend on the mathematical performance of digital signal processors (DSPs) or field programmable gate arrays (FPGAs) as typical 32bit microcontrollers, even those featuring floating point units, are not capable of calculating the next commutation point quickly enough at the highest rotational speeds.
Figure 2: TXZ devices include four key circuits that work together to provide sophisticated FOC-based motor control
To tackle this challenge, Toshiba has developed a vector engine (VE) peripheral block on a family of its microcontrollers (Figure 1). Inside the VE, the full complement of vector control equations are implemented as required for FOC. This customisable hardware block is complemented by a programmable motor drive (PMD) that generates the require pulse-width modulated (PWM) outputs and handles deadtime for the drive stage, together with an analogue to digital converter (ADC) that monitors the motor currents upon which the VE depends for its calculations.
Due to its reliance on hardware, the VE ensures stable and predictable code execution that is not impacted by the interrupts generated from other peripherals. Toshiba reports this results in up to a 70% faster execution speed compared to a pure software implementation that translates into support for significantly higher rotor speeds. Embedded development engineers are left with either more processing performance to execute other application code, or an opportunity to reduce power consumption by operating the processing core at a reduced clock rate.
The VE is integrated in the TXZ family of Arm Cortex-based microcontrollers (Figure 2). The TMPM4K devices use the Cortex-M4 processor with floating-point unit (FPU) operating at up to 80MHz, for application performance executed in conjunction with the motor control application. The PMD and ADC are tightly coupled with the Advanced Vector Engine Plus (A-VE+), allowing a certain degree of autonomous operation, while the ADC also offers 12bit resolution and a conversion time of 0.5µs using its own 120MHz clock.
The devices are offered in 7.0 x 7.0mm LQFP48 package, making them easy to integrate into compact motor control circuitry. Feature, such as oscillation frequency detection (OFD), a watchdog function and an emergency stop, provide safety functions.
Effectively delivering power
Motor control also needs to be supported by a competent driver stage to convert the three-phase complementary PWM output into the drive output for the motor. This will also contribute to the range design goals laid out by the e-bike development team. Toshiba also provides the UMOS IX low voltage (LV) family of MOSFETs, which focus on improving the three main parameters that affect the losses in power switching applications: gate charge (Qg), on-resistance (RDS(ON)) and recovery charge (Qrr).
Figure 3: RDS(ON) versus Qg has improved by 26% compared to previous UMOS technology generations
This lower RDS(ON) helps to reduce losses that would otherwise be transformed into heat that needs to be dissipated. The improved gate and recovery charge values deliver efficient operation when using fast switching. Despite these improvements, some heat is still generated which will have to be removed from the system.
Typically, bicycles provide ample heatsinking material in the form of their metal frames, if the mechanics of the design provide support for this approach. In addition, air movement due to the motion of the bicycle can also contribute to the cooling implementation. The thermal coupling of the MOSFET to its packaging, as well as the packaging itself, must also be considered as this will also have an impact on the available design approaches.
The DSOP Advanced packaging selected for the UMOS IX family is a surface mount package that provides thermally conductive metal heat spreading pads on its top and bottom sides. This allows for an effective thermal conduction and thermal performance while a 0.05mΩ reduction in internal package resistance helps to further improve the overall RDS(ON).
Toshiba’s TPWR6003PL is an N-channel MOSFET based upon UMOS-IX-H technology that is housed in a DSOP Advance package. It can be used in motor control within an e-bike as it supports drain source voltages (VDSS) of up to 30V. It is capable of delivering 150A of continuous current, or 500A when pulsed, and offers a channel to case thermal resistance of just 0.88°C/W. The wettable flanks, which are standard in DSOP Advance packages, enable the use of automated optical inspection (AOI) equipment to inspect the solder joints, ensuring they can withstand the vibration of e-bike applications.
Efficient HMI implementation
Beyond the technical specification of the e-bike, value-add technology can be the deciding factor for a consumer to purchase a specific model. This also needs to be sparing in its current draw so as not to impact on battery life. A Bluetooth interface allows e-bike developers to eliminate a display, for the rider to use a smartphone as the human machine interface (HMI). Using a suitable app, riders can visualise trip data, keep track of battery status, and link the daily commute to fitness apps.
Figure 4: Bluetooth enables riders to link e-bike status with smartphones and fitness apps
For high-end offerings, the Bluetooth interface could function as an additional interface to the e-bike’s application processor and colour display (Figure 4). In both cases, this could be implemented by a device such as the TC35680, which supports all major Bluetooth Low Energy 5 features, including its 2Mbit data rate, which allows for very fast transmission speeds between the user’s smartphone and the e-bike. This is particularly useful when a firmware upgrade is required.
The controller provides +8dBm transmission output through its built-in power amplifier for robust, reliable connectivity. Based upon an Arm Cortex-M0, it draws a peak current of 11.0mA during data exchange, with maximum deep sleep current of 50nA. The chip can be integrated into small form-factor displays, and includes the required RF matching circuitry. It comes with a qualified embedded Bluetooth stack so that developers can focus on adding their application software. For more complex user interfaces, the TC35680 can be connected via a serial UART interface to a larger application processor to add Bluetooth functionality. The software development kit (SDK) eases the addition of wireless connectivity.
Summary
E-bikes will continue to grow in popularity, help to contribute to worldwide efforts to reduce the number of fossil-fuel vehicles on roads and complement endeavours to move commuters to public transport alternatives. Key to success is the delivery of highly-efficient solutions that deliver good range and a safe, enjoyable ride. Through the selection of intelligent, optimised, motor control, coupled with advanced and efficient power devices, Toshiba is helping to bring successful e-bike designs to our streets and roads.
PCIM Euope - Visit Toshiba - Hall 9-301
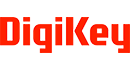