A guide to thermal impedance
This guide by Recom considers effective thermal impedance testing to allow the converter to run at full capacity, without compromising performance
All power converters dissipate power internally as heat but when the maximum internal temperature is reached, further increases in ambient temperature must be compensated for by reducing the amount of power dissipated inside the converter by reducing the load. This is called thermal derating.
The thermal impedance of a converter from case to ambient can be found from the equation:
If the power dissipation is known (the difference between the input power and the output power), then measuring the case temperature rise above ambient determines the thermal impedance.
Measuring the converter’s temperature rise above ambient has to be done with a very high precision. One way of increasing reliability is to make several measurements at different ambient temperatures, as the ΔT (temperature rise above ambient temperature) should be the same for each temperature step.
For true convection cooling operation, the thermal impedance has to be determined in a draught-free environment, as the air movement can influence the result. Placing the device under test (DUT) inside a cardboard box inside the temperature-controlled chamber and using a four-wire (Kelvin contact) system for terminal voltage measurements, ensures reasonably accurate measurements can be made. The wire mesh grid allows air movement while blocking draughts.
Figure 1: Thermal impedance test set up (DC/DC) using a thermal chamber
Thermal impedance is dependent on the efficiency with which heat is transferred to the surrounding fluid (e.g air). If the heat transfer co-efficient is poor, then the dissipated power will cause a greater increase in the case temperature and the thermal impedance will be higher. Equation 1 is only correct under convection cooling conditions.
It is also important that the testing conditions (documentation, equipment) stay constant to give reproducible results.
For most applications, the convection cooling thermal impedance figure is the most useful because this corresponds to the way that converters are soldered onto a circuit board and the heat dissipated inside the converter is then spread by free air convection cooling. Some heat will be conducted away via the electrical connections to the PCB tracks, so some temperature derating graphs given in the datasheets are accurate only if the PCB layout information is followed. A small amount of heat will be additionally dissipated by radiation to the surroundings.
The most effective way of increasing the efficiency of heat transfer to the surroundings is to move the fluid about.
Newton’s law of cooling states that for a given temperature difference, the rate of heat transfer can be increased by increasing the surface area (for example, by adding a finned heatsink to the DUT) or by improving the heat transfer co-efficient.
In practice, the heat transfer co-efficient typically changes abruptly at a boundary condition when the air flow over the converter transitions from laminar to turbulent flow. For most power converters with flat plate upper surfaces, this transition point is around 0.1 to 0.2m/s. Thus, an airflow of 0.1m/s (20LFM) can be considered to be convection cooled and anything higher can be considered to be forced air cooling (Figure 2).
Figure 2: Thermal impedance vs wind speed
Recom has its own in-house wind tunnel to accurately measure the thermal impedance of our products with forced cooling. The air flow inside the wind tunnel is laminar thanks to a honeycomb flow conditioner element and the output diffuser element eliminates back pressure variations, ensuring an even pressure and airflow profile in the central test volume.
A precision air flow sensor connected to a feedback circuit driving the fan guarantees a stable and accurately controllable air flow. The device temperature is measured using a thermal camera to avoid any turbulence effects caused by inserting a foreign object into the air flow close to the DUT.
The efficiency of a converter, in particular a PCB-mount module where the power density can be very high, is often a critical deciding factor when choosing the most suitable part. For example, a converter with 96% efficiency will have half the internal dissipated heat compared to a converter with 92% efficiency.
Testing provides accurate, temperature-based data and information for datasheets, such as thermal impedance and maximum case temperature figures, efficiency vs load tables and temperature derating graphs for standard parts and those with a heatsink option.
Testing allows designers to select and design-in the optimum part for an application, confident that the converter will function within its performance limits at cold (down to -40°C) and hot (up to 100°C) ambient temperature environments.
Steve Roberts is innovation manager of Recom Power
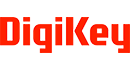