TE Connectivity surpasses face shield donation goal
TE Connectivity has produced more than 120,000 face shields to donate to medical workers around the world working the frontlines in the battle against COVID-19.
From Fremont, California, to Dinkelsbuhl, Germany, more than 360 TE employees at 12 sites logged in a combined 1,500 volunteer hours to manufacture, assemble and distribute the face shields, important personal protective equipment that has been difficult for many medical facilities to acquire during the pandemic.
TE’s initial goal was 100,000, but the volunteers kept working to fulfil continued requests from the medical community.
Leveraging open source designs, TE engineering and technology teams selected and modified a shield design by verifying the design with medical professionals to ensure that it was effective and comfortable.
“We received overwhelmingly positive feedback on our face shields,” said Phil Gilchrist, Chief Technology Officer, Communications Solutions. “I am proud of the creativity shown by the experts on our engineering, 3D printing and molding teams who quickly came together to work toward the common goal of protecting the medical community.”
The design and manufacturing process varied by region. While a few of the engineering teams used 3D printing to produce the face shield frames in the beginning of the initiative, many of the teams molded parts to accelerate production. Some of TE’s largest manufacturing sites could produce thousands on end, like the 70,000 shields that came from Central Pennsylvania. Other teams who did not have high-volume manufacturing capabilities through moulds used their 3D printing resources to produce face shields for their communities.
For example, the Medical group in Galway, Ireland, used its 3D printers to produce around 28 headbands per day and donated around 1,000 face shields to over 30 local destinations. Globally, TE face shields were sent to 137 medical facilities in the United States, 22 in Mexico and more than 100 across Europe.
Volunteers from departments throughout TE stepped in to assemble the face shields, including some who turned their own kitchen tables into workstations and made it a family project. The assembly process involved hour upon hour of hole punching, taping and other manual assembly tasks before they were swiftly prepped for shipping. These efforts, both big and small, helped outfit front-line medical workers in local communities around the world.
“In making these face shields, our employees turned to TE’s unique strengths as a company to help medical professionals at a time of unprecedented need,” said Kathleen Ambrose, Vice President of Global Government Affairs and Corporate Responsibility. “That level of dedication and engagement is something our communities and employees can be proud of and will remember long after this pandemic.”
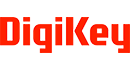