Understanding the value of power supply design verification and test
When the development of a product is starting to approach the stage when it will be released for manufacture, extensive testing is usually conducted.
This article originally appeared in the March'24 magazine issue of Electronic Specifier Design – see ES's Magazine Archives for more featured publications.
By Chris Maidment, Marketing Director, TDK-Lambda UK
This ensures that the product meets not only the published specification, but also complies with the appropriate safety and legal standards. This is usually referred to as DVT (design verification and test).
Prior testing may have already taken place as part of an Engineering Verification Testing process. This may involve the approval of a new part and will look at the design and electrical margins of all the components and materials used in the product.
It is unlikely that companies involved purely in the assembly of an electrical panel or fabricating equipment or a machine for internal use will go through this process. They will purchase parts from suppliers that they know or have used before. They trust the manufacturer to have performed their due diligence in thoroughly testing the item.
At first glance, an AC/DC power supply or DC/DC converter may seem a simple product. A PCB, transformer, two or three inductors, semiconductors, capacitors, and some connectors. How hard would that be to design, build, and perform some testing on?
Why does a power supply need extensive testing?
Extensive DVTs on a power supply are needed to ensure that not only the published specification is met, but also that its expected field reliability and lifetime are achieved. TDK-Lambda publishes the full test results online to help designers evaluate how much margin they have in their system and how it was tested. A thorough DVT can avoid problems manifesting in the field, which can tarnish the end customer’s reputation and involve significant costs to repair or service.
Potential capacitor failures
When a power supply is first turned on in cold temperatures, the output voltage may rise and fall repeatably, causing equipment to malfunction. This is because the cold ambient has reduced the capacitance in the housekeeping voltage and it cannot maintain operation. Testing at both high and low ambient temperatures will uncover this, and a higher performance capacitor may need to be used. Output voltage rise and fall characteristics are also measured at low-line (85Vac) and high-line (264Vac) inputs (Figure 1).
Figure 1. CUS250M-12 rise time characteristics
Measuring only selected electrolytic capacitor temperatures during the DVT and determining their lifetime can cause issues in short periods of time. After six months, a small control circuit capacitor can deteriorate to a point where the power supply fails to start. A full DVT report will show the life expectancy of all the critical capacitors.
After operating for a year or two, brief AC voltage interruptions may cause the power supply output voltage to fall, impacting the operation of the load. In this case, the electrolyte may have aged in the hold-up bulk storage capacitor, and it can no longer provide enough energy to sustain operation. A ‘Pass’ statement on a hold-up time test report will not indicate how much margin a power supply has.
Figure 2 shows the detailed hold-up information in the CUS250M-12 evaluation report. For example, at 100% load, the power supply output will hold up for around 28ms, twice the specification limit. This would give the user sufficient confidence that the power supply will not be impacted by short AC supply interruptions even after a period of time.
Figure 2. CUS250M-12 hold-up time
Minimal customer testing is highly unlikely to uncover these types of issues. Some power supply companies focused on a low operating cost model may need to invest more time and money in a detailed DVT.
The value of detailed test reports
Temperature measurements on convection-cooled power supplies are performed within an enclosure to simulate the end system conditions within which it will be mounted. Remember, capacitor lifetime can reduce by 50% for every 10°C rise in temperature. So cold air blowing from an air-conditioning vent above a test bench can easily reduce readings by 10°C and severely change lifetime forecasts.
A convection-cooled power supply needs about three hours for internal temperatures to stabilise. Temperatures should be measured at 85Vac, 115Vac, 230Vac and 264Vac inputs and with the power supply mounted horizontally, vertically, on its left, and on its right-hand side or even upside down. Thermal probes record and monitor the temperatures, and only when they have stabilised will they trigger automatic test equipment to change the voltage or rotate the power supply to the next thermal test.
Proactive product safety testing
TDK-Lambda UK Engineering has Certificates of Approval from UL for the Client Test Data Program and IECEE Customer Testing Facility (CTF) Stage 3 Program. New products are thoroughly evaluated to the safety standards prior to submission for official certification. This enables any issues to be rectified before the safety bodies perform their review. It also reduces the possibility that a product is not compliant with a safety standard.
Immunity and EMI testing
It is a legal requirement that a product meets both immunity and EMI standards and is mandatory for applying the CE or UKCA mark on a product. Many of TDK-Lambda’s engineering locations have internal testing facilities for radiated and conducted noise as well as the ability to test conformity for immunity, see Figure 3. Again, these results are detailed in the evaluation data, along with the test set-up used for measurement.
Figure 3. TDK-Lambda UK test chamber for radiated and conducted EMI
These resources have also been used to help customers solve their issues in conjunction with TDK-Lambda engineering assistance.
Extensive DVT allows for longer warranties
An extensive Design Verification and lifetime calculation for the capacitors allow TDK-Lambda to offer extended warranties with minimal risk to the company. A longer warranty gives the customer a lower ownership cost and a higher level of confidence in the product’s field life.
Design verification also involves measurement and validation of the mechanical aspect of the product. This is less likely to produce issues with today’s CAD (Computer Aided Design) software, 3D modelling and the use of that data to program metal forming machinery or even additive manufacturing (3D printers) equipment.
Summary
A very thorough design verification on a power supply allows detailed reports to be published or shared. It gives valuable information to the potential user on how a product will operate in the future. It also allows a company to demonstrate confidence in why a long warranty can be offered and provide a lower cost of ownership.
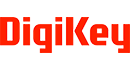