Vehicle electrification revolution enters a new era
The electric vehicle (EV) revolution is leading the automotive industry into a new age. New vehicles will have an electric powertrain option or come as a standard offering, thanks to advances in technology and power generation. Car makers are adding more EVs to their lineups while setting goals for carbon neutrality and bold electrification strategies. Marc Bracken, Technical Marketing Engineer – Automotive Systems Engineering, ON Semiconductor, explains.
Many governments are enacting limits to help reduce CO2 output from the transportation sector, making the electrification of the powertrain a prime focus for all vehicle original equipment manufacturers (OEMs). The momentum from these enacted laws and the general commitment to the Paris Agreement is motivating change. This commitment will limit the rise in the global average temperature, with a goal of keeping it less than 2°C above the level in pre-industrial years. This will only happen with a reduction in total CO2 emissions and the move to e-mobility is a major part of that effort.
There are many aspects to this historic watershed moment. This series of articles will aim to cover a variety of solutions for EV, but the starting point really needs to be the battery electric vehicle (BEV), also known as the zero-emission vehicle (ZEV). In the US, the average daily commute distance is less than 30 miles, or 48km roundtrip. The typical range of a BEV today varies by the size of car and its position in the market, whereby luxury vehicles tend to have a higher range than non-luxury models. Ambient temperature also affects range, with most cars achieving greater range during hot summer months than cold winter periods.
There are many use cases where it makes sense for consumers to move to a BEV solution. BEVs have an average range of around 200 miles, or 320 km, and can easily handle the daily commute as well as weekend leisure activities on a single weekly charge. The great appeal here is that recharging a BEV costs much less than refueling an internal combustion engine (ICE) vehicle. The main environmental benefit of a BEV is that for the weekly commute there is no emission of CO2 from the vehicle, whereas for an average commute of 30 miles an ICE would generate 12kg, or nearly 28lbs, of CO2. According to the US Environmental Protection Agency (EPA, 2021), the average passenger car releases 4.6 metric tonnes of CO2 into the environment in a year. When considering the number of vehicles on the road worldwide, that equals over 6.4 billion metric tonnes of CO2 released every year. Countries are enacting limits to help reduce CO2 output from the transportation sector, making the electrification of the powertrain a prime focus for all vehicle original equipment manufacturers (OEMs). For perspective, the annual CO2 output from vehicles is equivalent to the annual CO2 output of 1,000 power plants, based on estimates from the EPA.
BEVs will make up approximately 35% of all EVs produced in 2026 (Strategic Analytics, 2020). A BEV involves a completely new powertrain, one that replaces the engine, gearbox and even the differential gears in the axle. The electric powertrain replaces those systems with one or several electric motors that provide traction, and in most cases, do not require additional gears. In an ICE powertrain, complex mechanical systems are necessary to reduce the high-speed revolutions of the engine down to the much lower, but high torque, drive that is applied to the wheels. A BEV allows for much greater finesse using control electronics, which drive the motor. The torque is available even at low revolutions and the motor is capable of spinning at very high speeds, often requiring no additional gearbox. The BEV replaces the ICE with an electric powertrain, replaces fossil fuels with a lithium-ion battery pack and refuels by charging the battery pack from the electrical distribution grid.
Above: Figure 1. Electrification Classification for EVs in 2026 (FCEV = 1%, not shown)
This flexibility for electric motors does come with some conditions, of course, in the form of distributing power within the system. The battery voltage in a BEV is high, in the region of 400V to 800V DC. High power electronic solutions are required to charge this high voltage battery pack as well as to power the traction drive in BEVs.
Charging the battery pack requires the use of an on board charger (OBC) or an off board DC fast charger. The OBC must convert an AC input, which may come from a single-phase or 3-phase source, to a high voltage DC output to charge the battery. The OBC must also employ power factor correction (PFC) in order to minimize the reactive power drawn from the AC grid. Another way to charge the BEV battery pack is to use a DC fast charger. DC fast chargers are part of commercial energy infrastructure installations and are stand-alone units that are not on the vehicle. DC fast chargers are much higher power than an OBC and bypass the OBC to charge the battery directly. However, DC fast chargers still have the same basic function of converting the AC input source to a high voltage DC output while employing power factor correction.
The traction motors in a BEV are normally AC induction, and the high voltage DC battery source cannot drive this directly. The traction inverter module, which may require an external boost or have the boost function integrated, must take the high voltage DC source and provide 3-phase or 6-phase sinusoidal drive waveforms to the electric motor. These drive waveforms are controlled to increase the torque and speed of the traction motor. Another important function of the traction inverter electronics is to perform energy recovery while coasting or braking. When the vehicle is in motion, and there is no active acceleration input from the driver, the traction motor behaves like a generator. The vehicle’s momentum spins the traction motor, and the traction inverter electronics reverse the power flow providing energy back to the high voltage battery pack.
Vehicle electrification is not new, but the emphasis on large-scale adoption across vehicle manufacturers has never been this elevated. It is a rapidly changing and evolving sector, with new technologies developed all the time. While there are challenges to solve, continual improvements in electronics efficiency, charging time, battery chemistry, charging infrastructure and lithium resource extraction are all occurring. Energy storage, in the form of rechargeable batteries for BEVs, is a major area of research. Advancements in battery design and cost structure will dictate how aggressively the average selling price of a BEV will come down, and design improvements will improve storage capacity.
Increasing the storage capacity will improve range, but to realise the full storage capabilities of the battery one cannot ignore the need for greater system efficiency. Two high level items are evident when considering efficiency in a BEV powertrain. The electric powertrain must be able to use the maximum amount of battery capacity, it must be able to charge the battery quickly, and both must occur while minimising thermal losses.
The power electronics required for a BEV powertrain contribute to the overall system efficiency. Without optimal efficiency, the system loses valuable energy from the battery or the grid in the form of waste heat. One technology is proving to be extremely important in this respect. Silicon Carbide (SiC) is displacing or enhancing standard silicon power semiconductors used for traction inverters, DCDC converters, OBC and DC fast chargers. ON Semiconductor is leading in this area, with a growing portfolio of high power SiC MOSFETs, SiC diodes, hybrid IGBTs and Automotive Power Modules (APM). SiC solutions provide higher power density, higher voltage breakdown and increased reliability while improving overall system efficiency. Additional technologies for vehicle electrification in its product line-up include Super-Junction MOSFETs, IGBTs and solutions for low voltage power regulation, analog signal chain (sensing) and In-Vehicle Networking (IVN).
Above: Figure 2. EV/HEV growth for the next five years
The automotive industry is pivoting and the momentum behind electric vehicles is strong. This will encompass all classes of light and commercial vehicles. Some believe electrification will come to mass transport and road logistics sooner than the consumer end of the market, and there is good reason for this. Mass transport allows amortization of the cost across many more individuals, while last-mile delivery has particular requirements that fit very well with electric powertrains.
New technologies, typified by SiC solutions from ON Semiconductor, will accelerate this trend, giving it even greater momentum. Advancements in range, charging time, environmental impact, cost of ownership and consumer satisfaction will drive us towards an electric future. The global initiatives provided by legislation will further motivate automotive manufacturers towards developing the new vehicles needed to make the transition complete. In many instances, this is already happening. The expected EV/HEV compound annual growth rate (CAGR(VOL)) will be 20.1% from 2021 to 2026 and BEVs will be 29.7% (Strategic Analytics, 2020).
ON Semiconductor is an important part of that value chain, providing key enabling technologies to support this electric powertrain revolution. Our solutions help customers to design high-end systems that address an array of power tiers while maximising power density, efficiency and reliability.
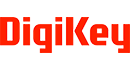