Protecting automotive 10BASE-T1S Ethernet networks
As modern vehicles have become more connected and reliant on electronic systems, the adoption of automotive Ethernet has steadily risen across OEM platforms. But technology never stands still – and engineers are always looking at ways to develop this networking to ensure it is fit for the future.
This article originally appeared in the Oct'23 magazine issue of Electronic Specifier Design – see ES's Magazine Archives for more featured publications.
The emergence of 10BASE-T1S
Ethernet was initially designed for multi-drop networks, with data transmitted using carrier sense multiple access with collision detection (CSMA/CD). While this best-effort delivery technique met the networking requirements for general-purpose computing, its non-deterministic nature (i.e., data delivery could not be guaranteed within a specified time interval) caused by packet collisions meant multi-drop Ethernet networks could not be used in real-time applications where safety was paramount. As more safety features like advanced driver assistance systems (ADAS) were added to new vehicles, this limitation became increasingly problematic for the automotive industry, which was also looking for ways to transition to a new zonal architecture.
Connectivity in zonal architectures is based on physical location rather than function, which is used in domain-based architectures. This has the advantage of reducing the number of electronic control units (ECUs), which reduces the size of the wire harness. Furthermore, it eliminates the reliance between hardware and software, enabling a service-orientated architecture (SOA). 10BASE-T1S was developed to address the requirement for reliable and deterministic high-speed data communication in the automotive (and industrial) sectors. It was published as IEEE 802.3cg as part of its Time-Sensitive Networking (TSN) series of standards.
10BASE-T1S differs from other automotive Ethernet technologies because it supports multidrop topologies where all nodes are connected using the same unshielded twisted pair cable.
Since bus implementation only requires a single Ethernet interface (PHY) at each node (removing the need for a switch or star topologies associated with other forms of automotive Ethernet), it is lower cost. While the standard specifies support for at least eight nodes, it can support many more over bus lengths of up to 25 metres. Another new feature of this standard is physical layer collision avoidance (PLCA), which prevents collision on the shared network medium. This ensures deterministic maximum latency depending on the number of network nodes and the amount of transmitted data. Each node is allowed to transmit. If it has no data to transmit, it passes the transmit opportunity to the next node, enabling more efficient use of available bandwidth.
10BASE-T1S networks are AC-coupled, meaning they also support power delivery. This saves cabling and reduces connector sizes, thereby increasing overall network reliability. Power over data lines (PoDL) is already available for point-to-point implementations, and the IEEE is currently working on standardising this feature for multidrop topologies. Table 1 presents the physical layer features of 10BASE-T1S.
Protecting 10BASE-T1S networks: challenges and solutions
While Ethernet provides excellent link robustness, deploying it in an electrically noisy environment, like an automobile, presents additional challenges. Motors used to drive electric vehicles (EVs) are sources of radiated or conducted EMI noise. EMI and electrical transients are noise sources that can significantly impact high-speed data transmission. While twisted-pair SPE cables are designed to reduce the effects of common mode noise, some induced noise will inevitably occur.
There are different categories of conducted and radiated noise. Common mode noise appears as a signal superimposed on differential input and output terminals and positive and negative power supply voltage rails. To mitigate common mode noise while preserving uninterrupted transmission of desired differential signals, common mode chokes (CMC) composed of two windings encircling a ferrite core are frequently employed.
Differential mode noise signals flow in opposite directions and can be suppressed using a suitable filter consisting of an inductor, capacitor, or differential mode choke. Electrostatic discharge (ESD) can result in transient voltage spikes (large dV/ dt) that can induce damaging high voltages onto cables, damaging semiconductors, and other components. Voltage-dependent resistors (varistors) or transient voltage suppressors (TVS) can help to protect against the potentially harmful effects of ESD. Figure 1 illustrates how a typical multi-drop 10BASE-T1S network connecting several ECUs in an automobile is protected using a combination of CMCs and varistors.
Implementing SPE protection
Since 10BASE-T1S adopts a multi-drop connection with many ECUs connected on a single bus line, signal reflections inevitably occur due to the length of the wire harness. In addition, the extra capacitance introduced by multiple ECUs can cause ringing on the data signal. Furthermore, due to the nature of electronic components used in differential communication lines, the conduction mode can sometimes be converted from differential mode to common mode or vice-versa. This is called mode conversion.
Mode conversion causes differential signals to be converted to noise or noise to be converted to differential signals, resulting in poor noise immunity at the ECU, potentially causing it to malfunction or emit even more noise.
These issues arise due to asymmetries (differences in inductance and capacitance) in differential communication lines. For automotive Ethernet, mode conversion characteristics (Sdc11, Ssd21, Ssd12); return loss (Sdd11); and insertion loss (Sdd21) are generally used for component selection and ECU design. Standard lines (Sdd11, Sdc11) have been established for these S (scattering)-parameters in IEEE802.3cg. Therefore, the S-parameters of individual and combined components are essential indicators when designing ECUs.
The ACT1210E series of common mode chokes/filters from TDK is the industry's first for automotive Ethernet 10BASE-T1S. These devices use TDK's proprietary wire winding structure and optimal materials to achieve industry-leading S-parameter values (Figure 2).
Laser welding winding wires to the metallising terminals provide these products with high thermal shock resistance and high reliability over an operating temperature range from -40 to +125°C. Table 2 summarises key features of TDK’s recommended ACT series CMCs for automotive networks, which comply with 10BASE-T1S EMC test specifications.
Table 2. Recommended CMCs to mitigate common and differential mode noise in automotive networks. (Source: TDK; recreated by Mouser Electronics)
Similarly, ESD-mitigating components also have stringent specifications, including lower capacitance and narrower tolerance requirements than standard ESD components. The TDK AVRH10C101KT[1]1R2YE8 and AVRH10C221KT1R5YA8 chip varistors, part of the AVR-H varistor family, offer high ESD protection performance and have a maximum capacitance of only 1.5pF (typical) with a narrow tolerance of ±0.13pF (Table 3). Additionally, the AVR-H varistors offer enhanced robustness with high operating temperatures of up to 150°C without derating performance. These varistors provide ECU network designs with high ESD immunity while having minimal impact on communication quality and mode conversion characteristics. They also comply with the AEC-Q200 automotive reliability standard, making them suitable ESD protection components for 10BASE-T1S automotive Ethernet applications. The interline stray capacitance and mode conversion properties of these CMCs make them ideal for 10BASE-T1S installations.
Making automotive networks reliable and robust
In conclusion, multi-drop 10BASE-T1S will play a central role in supporting the deployment of zonal architectures on next-generation vehicles. But ensuring network reliability and robustness in a way that does not affect factors such as bandwidth and latency remains uppermost in engineers’ minds. High-quality noise filtering and ESD protection solutions are necessary to achieve this aim. This article outlined sources of electromagnetic noise and voltage transients that can impact Ethernet network performance.
TDK offers automotive-compliant CMCs and varistors/TVS to protect 10BASE-T1S networks, as well as to protect other forms of automotive Ethernet (e.g., 100BASE-T1) and other legacy automotive networks. The protection components highlighted in this article are all available from Mouser Electronics, an authorised TDK distributor.
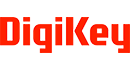