Digital transformation - friend or foe?
Industrial automation; digital transformation; Industry 4.0; the IIoT. These are all buzzwords that us in industry should be more than used to hearing by now. But, what do they actually mean in practice? On a visit to Analog Devices’ (ADI’s) Limerick headquarters, Electronic Specifier spoke to the Vice President of the company’s Industrial Automation & Energy Group, Kevin Carlin, who answered the question of whether we should look at digital transformation as a friend or foe.
There is a significant amount of negative rhetoric out there when it comes to digital transformation and we’ve all seen the ‘robots are coming to take our jobs’ style headlines. As such, when speaking about automation it isn’t long before the conversation turns to whether or not people will be put out of work.
There’s no doubting the pace of global change over the past decade and we’ve seen first-hand the pros and cons of globalisation from the upside of the rapid rate of innovation to the undeniable downsides such as climate change.
However, as Carlin explained ADI take a more optimistic view of the landscape and was keen to highlight the opportunities created by the digital transformation. “We’ve all seen headlines over the last few years about how robots are coming to take European jobs,” he said. “In my view that overshadows the opportunities that these sorts of systems can bring to companies in terms of their competitiveness, productivity, and ability to drive efficiencies.”
Consumer demand
Globalisation has totally changed us as consumers – we now expect higher quality; a greater variety of products; an increased level of customisation; and delivery expectations of hours rather than days. This in-turn has forced manufacturers to rethink their strategies.
Traditionally manufacturing architectures have been largely centrally located, fixed and not particularly scalable or flexible. This creates a model where manufacturers became adept at producing small numbers of products but in high volume.
The classic and well-known example of course is that of Henry Ford when he introduced this premise to mass production – which has since been replicated for decades. His famous quote about consumers buying his Model T Ford was that: “they could have any colour, as long as it’s black.”
However, this ethos doesn’t quite stack up when compared to the consumer demands of the 21st century. Continuing with the automotive analogy Carlin added: “If you go to the BMW or Audi website, you will be able to select thousands of different configurations and they’ve got to be able to monitor and view how the demand for one particular model changes from another over a certain time period. What models are in demand? Do they have to build new factories or reconfigure current factories?”
ADI has been observing this shift and manufacturers are starting to embrace the idea of the digital world and IoT, and they are responding by upgrading their manufacturing footprints to allow for more configurability, flexibility, and modularised automation equipment that can be scalable and moved around. This allows them to respond in real-time to these demands and ship higher quality products faster.
Opportunity knocks
Carlin added that digital transformation is introducing a whole host of new opportunities for automation, robotics and communications systems which in-turn opens up opportunities in IoT and Industry 4.0.
He added: “The first industrial revolution was the introduction of steam power; the second was the emergence of electric motors; the third was the introduction of computers. Now, it is harnessing the power of the internet and real-time data and bringing that into the factory.”
Like with the industrial revolutions that preceded it, Carlin further explained that, initially, this was a scary proposition. For the 19th century factory worker, who first clapped their eyes on a steam powered machine, it must have been a daunting experience. Likewise, for manufacturers Industry 4.0 means opening up the plant to the outside world, where previously there would have been contained, fixed, and rigid architectures which are customised to run efficient operations at machine level.
Carlin added: “When you start fiddling with architecture, introduce IT networks and Ethernet connections, and try to pull data up to the enterprise level, it can be difficult.” This is often complicated still further when IT and OT professionals work together as they often have very different agendas.
Undoubtedly Industry 4.0 and the Industrial Internet of Things (IIoT) has opened up a number of challenges, and to make it a reality it means the deployment of more sensors across the ecosystem; more robots operating close to humans (and thus the requirement for safer environments); machine vision cameras to provide real-time visualisation; and the need for easy reconfiguration of systems.
How do manufacturers achieve all that with their incumbent systems, legacy cables and protocols? And what happens if an increased level of data is all of a sudden dumped onto a network which is already highly optimised and configured?
“It’s really important to figure out solutions to these challenges as the consequences when something goes wrong can be catastrophic,” warned Carlin, “not just in terms of productivity down-time but also in terms of security and personnel safety.”
With this significant legacy infrastructure, manufacturers could be forgiven for being slow to move, and it would be foolish to think that they would rip the heart out of their operations and replace it with all this cool digital IoT technology and everything would be fine.
“We understand this market well enough to know that you can’t just switch it on and off – you’ve got to find a way to allow this industry to transition,” said Carlin. “As ADI our biggest challenge is to help them do that by solving their biggest problems, and accelerate that transition? That is where we are focused and that’s where we have decided to invest. Europe is very important for ADI as it’s the birthplace of Industry 4.0, and we have an entire investment strategy around it.”
Benefits
Earlier we touched upon some of the downsides of globalisation, but it’s here that Industry 4.0 can have a real positive impact. Carlin highlighted that around 50% of energy related carbon dioxide emissions comes from the industrial sector, with 40% coming from electric motors. Therefore, if variable speed drives were employed to power these motors more efficiently it would be a huge weapon in the battle against climate change.
The World Economic Forum (WEF) reported as recently as January that digital technology is expected to reduce global greenhouse gases by up to 15% by 2030 – that represents a bigger carbon footprint than the US and Europe combined, and Industry 4.0 will accelerate that process.
Despite the fears over robot invasion there are still many tasks that will need to be completed by humans. For an operator in a manufacturing plant in Europe today, working on a repetitive task, there’s a fairly good chance that their job is going to be replaced by a robot or cobot.
Carlin added that depending on the task, that is no bad thing, and employers are beginning to find retraining opportunities and more interesting and rewarding tasks for the human workforce, allowing these ‘cobots’ to take over some of the more repetitive tasks. Indeed, the dangers of sustained periods performing mundane tasks is not to be underestimated and there have been unfortunate instances of worker suicide in China over the last few years.
So, what does this mean for ADI? You need a lot of technology to allow those robots to exist and operate next to a human. For example, the vision of a traditional automotive manufacturing facility will feature large robots behind safety cages, kept well away from human interaction.
However, in the world of Industry 4.0 humans will be working in close proximity with these cobots. This will require high speed real-time communications, precise control techniques, sophisticated proximity and depth sensing. And this, said Carlin, is where ADI can play a key role. For example, a European automotive manufacturer employed a condition monitoring solution from ADI, which then reported an anomaly on its turntable chassis welding.
When the issue was investigated further it was discovered that there was a badly damaged gearbox on the brink of failure. Repairs were planned in advance and took place during a scheduled down-time period, meaning that there was no production down-time and the company saved approximately €2m.
So despite the fact that the employment drum is still being banged with regularity, the statistics suggest that there will be a lot of job creation brought about by Industry 4.0 - with every new technology job creating another five in the local non-tradable sector. Carlin added: “Perhaps not in the plant itself, but there’s a huge ecosystem around a successful plant that includes a whole economy of startups; partners and service providers; and new business model designs.
“Indeed, in terms of economic growth evidence suggests that Industry 4.0 alone will generate an additional €30bn in Germany, and if you extrapolate that across all of Europe you could be looking at an additional annual revenue increase of around $100m.”
Why ADI?
Carlin concluded: “We have deep domain expertise, so we’ve hired people from the industry, work very closely with our customers and we recognise the main challenges that they face. And we can tap into the whole breadth of technology that ADI bring to the table – right from the precision signal chains to digital isolation technology; from power management to connectivity.
“We’ve also introduced new networking capabilities - all part of this new wave of innovation that is enabling Industry 4.0. All of this additional data and bandwidth is to be introduced to the network, increasing to higher speeds, and enabling digital communication all the way from the edge to the sensor level of the network.”
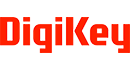