Software selectable over a single connector
While the RS-232, RS-422, and RS-485 serial standards are hardly new, combining them over a single connector creates challenges unforeseen when these standards were first drafted years ago. Jack Roan, Product Marketing Manager for Connectivity products at Exar, explores solutions in this article from ES Design magazine.
The RS-232 serial standard was first introduced in 1962 to connect teletypewriters with modems, printers, and other peripheral devices. In the years since, additional serial standards such as RS-422 and RS-485 emerged, offering higher data rates, improved noise immunity, longer transmit range, and multi-drop and multi-node bus communication.
While legacy protocols have largely been replaced by USB in the personal computer market, RS-232, RS-422 and RS-485 are still used heavily in industrial applications like medical devices, factory and building automation, and robotics. These protocols are simple and low cost to implement, are time tested and deliver rugged and robust communication in noisy environments..
Interfacing with an existing network of serial devices may require several of the common protocols, typically with separate external connectors for each. However, with the electronics equipment industry continuously moving in the direction of cheaper, smaller, and quicker to market, designers are being pressed to reduce the number of bulky connectors and deliver a lower cost integrated solution in a shorter time. Since the RS-232 standard specifies the DB9 connector, it is often chosen, requiring the RS-485 and RS-422 standards to co-exist alongside RS-232 in the same connector.
Integrating multiple serial standards over a single shared connector introduces a host of issues the standards developers did not conceive or plan for. Proper signalling with one protocol requires the drivers and receivers of the others to be disconnected to avoid excessive loading on the bus. Many standalone RS-232 or RS-485 transceivers offer standby or tri-state modes, but do not completely disconnect from the bus. This creates a long term reliability concern, as legacy RS-232 devices can drive signal levels up to ±15V, which could damage RS-485/422 devices that are only tested from -7V to +12V.
Figure 1: Block diagram of the SP388
Older and lower cost RS-485 transceivers require external biasing resistors to hold the bus in a known state when transmitters are idle or powered off. The RS-232 protocol was not designed to drive these resistive loads, so they must be removed from the lines for RS-232 communication. Also, the RS-485 and RS-422 standards specify a termination impedance at each end of the bus to reduce signal reflections at higher data rates. Switching these cable terminators and biasing resistors in and out of circuit requires bulky and costly relays, due to the range of common-mode voltage that the RS-485 standard allows.
Integrated solutions
Multiprotocol serial transceivers combine RS-232, RS-422 and RS-485 drivers and receivers into a single chip to address these common issues. For example, the SP338 and SP339 devices from Exar (Figure 1) include switchable termination resistors for high speed RS-485/422 (up to 20Mbit/s) and full support of all eight RS-232 signals specified for the popular DB9 connector (Table 1). They seamlessly handle the impedance switching necessary when sharing a single connector and communication bus with multiple serial standards, and do not require any external resistors or switches. The on-board charge pump generates the RS-232 bipolar voltage levels from a single 3.3V or 5V supply with only four external capacitors, and does not require any inductors or magnetic components. Packaged in 40 QFN, these devices are significantly smaller and much easier to implement and control than multiple discrete transceivers for each protocol.
Figure 2: Supporting multiple protocols through a single DB9 connector
Industrial serial designers can now use these highly integrated, multiprotocol devices to save board space, increase functionality, and provide more reliable communication. A small innovation in the world of industrial design, but a cost and time-saving innovation that designers will appreciate.
Multiprotocol transceivers with integrated termination resistors greatly simplify the development of modern serial controllers, resulting in smaller, lower cost, and quicker-to-market solutions.
Table 1: Supported DB9 connections and protocols using Exar’s multiprotocol transceivers
Author profile: Jack Roan has been Product Marketing Manager for Connectivity products at Exar since 2009. In the past 12 years he has held a variety of design, marketing, and field applications roles within the wireless and semiconductor industries. Jack has a BSEE in Engineering Physics and an MSEE in RF/Analog Integrated Circuits and Systems, both from the University of California, San Diego. He holds three patents in the area of digital power supply regulation.
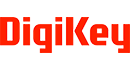