Putting the head in the cloud
The development of wireless vibration sensors is enabling a shift towards cloud-based predictive maintenance.
By Bob Scannell, Analog Devices.
Manufacturers are increasingly focusing on factory automation to improve efficiency as it can offer an increased bottom line and reduced costs from equipment downtime. Rather than relying on complex methods to predict maintenance needs, process control and predictive maintenance program developers can use wireless vibration sensors to enable accurate real-time sensor-to-cloud analysis and controls.
Issues such as imbalance, defects and other anomalies in the manufacturing process can inevitably lead to productivity losses where equipment must be taken off the assembly line due to loss of precision, inefficiency and safety concerns. Even slight shifts in equipment performance can quickly translate into measurable lost productivity. Therefore process monitoring and condition-based predictive maintenance are essential. Yet, the existing methods have limitations, particularly when it comes to analysing the vibration data and isolating error sources.
Factory process control and maintenance automation represents a high-value target for wireless sensing networks. The ideal solution is a complete detection and analysis system that can be embedded in the machinery and either act autonomously, or seamlessly interface with cloud-based computing. Before implementing such a system, it is important to understand and consider the factors that affect the data collection process.
Accurate and repeatable measurement
Existing handheld vibration probes do not require any modification to the end equipment and are also relatively highly integrated, given their large size. One major drawback, though, is the lack of repeatable measurements and reliability. Slight differences in the probe location or angle will produce inconsistent vibration profiles, making time comparisons inaccurate. Therefore, the maintenance technician is left wondering whether any observed vibration shift is due to an actual change within the machinery or just a change in the measurement technique.
Process monitoring can be particularly valuable in a production facility for high-value equipment where subtle shifts in the assembly line may lead to reductions in factory output, and critical end-equipment specification shifts. However, an obvious limitation of the handheld probe, and most piezo-based sensors, is the lack of real-time notification for inaccurate vibration shifts. In contrast, an autonomous sensor processing system that includes sensor, analysis, storage and alarm capability all in a small form factor delivers the fastest notification of vibration shifts and can best show time-based trends.
Understanding the data
It is only possible to gain real-time notification from an embedded sensor if frequency domain analysis is employed. Any given equipment typically has multiple sources of vibration. Time-based analysis of the equipment produces a complex waveform, providing little discernible information.
Most piezo-based sensor solutions therefore rely on off-line post-processed analysis of the Fast Fourier Transform (FFT) analysis, with no real-time notification and a difficult design burden on the equipment developer. With embedded FFT analysis on the sensor, vibration shifts can be isolated to specific sources immediately. Adding a fully integrated sensor also can reduce development time for equipment designers by 6-12 months.
Most vibration sensor solutions in use today are analog output only, leading to signal degradation during transmission and complex offline data analysis. Embedded FFT analysis assumes that the analog sensor data has been conditioned and converted to digital, to support simplified data transmission.
Given that most industrial equipment requiring vibration monitoring tends to exist in noisy, moving, inaccessible and even dangerous environments, there is a strong desire to reduce the complexity of interface cabling and to perform as much of the data analysis at the source to capture the most accurate representation of the equipment vibration. A wirelessly enabled sensor node facilitates immediate access and greatly simplifies the deployment of the sensor network at a significantly reduced cost.
Many existing sensor solutions are single-axis piezo transducers. These piezo sensors provide no directionality information, so they present a limited understanding of the equipment vibration profile and in turn rely on very low-noise sensors to enable the necessary discernment. Using multi-axis MEMS-based sensors increases the ability to isolate the vibration source, while also potentially improving cost.
Location and distribution of sensors
The question of where to place sensors is critical, as equipment vibration profiles are complex, time-shifting, and susceptible to variances based on the equipment materials and location. In addition, with the high cost of sensor elements limiting the number of probe points to one or a few, this question is even more critical. However, positioning is also highly dependent on the type of equipment, the environment, and even the life cycle of the equipment.
This means either significant upfront development time is necessary to determine optimal placement through experimentation, or it compromises the quality and amount of data to be captured. Conversely, a fully integrated sensor allows placement of multiple probes per system, lower development time/cost, and potentially fewer and less costly sensors.
With proper oversight, a handheld monitoring system approach can accommodate changes in scheduled maintenance (periodicity, amount of data, etc.) over time. Providing that same life-cycle based customisation in an embedded sensor requires upfront attention during design and deployment to allow the needed tunability. The transducer component, regardless of technology, is important but sensor conditioning and processing wrapped around the transducer is typically more critical. The signal, sensor conditioning and processing can be specific to unique equipment and life cycle needs. This translates to several important considerations in sensor design.
Earlier analog-to-digital conversion (i.e., at the sensor head versus off-equipment) allows for configuration and tuning in-system. The ideal sensor would provide a simple programmable interface that would streamline equipment setup through quick baseline data captures, manipulation of filtering, programming of alarms, and experimentation with different sensor locations. With existing simple sensors, some sensor settings must be compromised to accommodate changes in maintenance concerns over the life of the equipment.
It is possible to adapt the sensor to changes in equipment life cycle if the baseline equipment response is known. Even simple analog sensors can allow this, assuming the operator takes measurements, performs the offline analysis, stores this data offline and somehow properly tags to the specific equipment and probe location.
A preferred and less error-prone approach would allow baseline FFT storage at the sensor head, eliminating any potential for misplaced data. The baseline data also helps with establishing alarm levels, which again would ideally be programmed directly at the sensor. Therefore, in any subsequent data analysis and capture where warning or fault conditions are detected, a real-time interrupt can be generated.
Within a factory, a proper vibration analysis program may be monitoring tens or even hundreds of locations, whether by handheld probe or embedded sensor. Over the course of a given piece of equipment’s lifetime, this may produce the need to capture thousands of records. The integrity of the predictive maintenance program depends on the proper mapping to location and time of the sensor collection point. For the lowest risk, and the most valuable data, the sensor should have a unique serial number and the ability to time stamp the data, in addition to embedded storage.
Reliability
This discussion highlights methods to improve existing sensor-based approaches for vibration monitoring related to process control and predictive maintenance. What if the sensor becomes faulty (performance shift) rather than the equipment? With many transducers, such as piezo-based, this presents a serious limitation, as they have no means of providing any sort of in-system self-test.
There is always a lack of confidence in the consistency of data recorded over time. In the end-of-life critical monitoring phase where real-time fault notification is time and cost critical (not to mention a significant safety concern), there is always a concern that the sensor could become non-functional. An essential requirement of a high-confidence process control program is the ability to remotely self-test the transducer. Fortunately, this is possible with some MEMS-based sensors.
The ADIS16229 digital MEMS vibration sensor with embedded RF transceiver from Analog Devices is an example of a fully autonomous and wireless frequency domain vibration monitor. It features embedded frequency domain processing, a 512-point real-value FFT, and on-board storage, providing the ability to identify and classify individual sources of vibration, monitor their changes over time, and react to programmable threshold levels.
The MEMS sensor provides a digital self-test mode to provide continuous confidence in functionality and data integrity. The device is fully embedded and programmable, enabling placement close to the vibration source and early detection of small signals in a repeatable way, avoiding data discrepancies due to differences in location/coupling from measurement-to-measurement, which can be the case when using handheld devices.
A proprietary 902.5/927.5MHz wireless protocol interface allows the ADIS16229 sensor node to be remotely located. The ADIS16000 gateway node provides a standard serial peripheral interface (SPI) to any system controller device, supporting the ADIS16229. Up to six remote sensor nodes can be controlled via the gateway.
The ADIS16229 MEMS-based sensor node offers a 902.5/927.5MHz RF link to the ADIS16000 gateway controller. Six remote sensor nodes can autonomously detect, collect, and process data and wirelessly transmit it to a central controller node. Fully integrated and reliable vibration sensors, capable of autonomous and configurable operation, provide process control and enable predictive maintenance programs to significantly improve the quality and integrity of the data collection process, without the limitations and compromises posed by past vibration analysis approaches.
With the high level of integration and a simplified programmable and wireless interface, these sensors can enable a more pervasive deployment of vibration sensing. Such fully integrated sensors, which do not depend on retrofitted wiring/infrastructure and also detect performance shifts more precisely and reliably, offer the opportunity to drastically reduce upfront and recurring maintenance costs.
Moving from the model of hand-held and periodic vibration monitoring to embedded and continuous monitoring, coupled with cloud based analytics, provides a multiplying effect on the intelligence and expertise in the equipment monitoring field as it exists today. With more reliable and capable sensor nodes enabled by MEMs approaches, this sensor-to-cloud model will help realise the long awaited full potential of real-time condition based predictive maintenance.
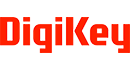