Power
Thermal management for Cool-Power isolated DC-DC converters
Communications and storage equipment designers remain under constant pressure to increase system performance whilst using less board area and smaller form factors. Improved power system density can make a significant contribution to this goal by freeing up board space for system-level features.
VicoThe PI3101’s efficiency remains consistent irrespective of its supply voltage, and is 85% or better with a 10 A load. At 15 A and above this efficiency reaches 87%. However, as with all power systems, the maximum available output power degrades as ambient temperature increases, so effective thermal management must be used to realise the device’s full potential.
A thermal management strategy has two key tools at its disposal; the use of heatsinks, and forced air cooling. It is possible to operate a PI3101 with neither, and in some circumstances where the power demand and ambient temperature are moderate, this may be the best solution. In other situations, heat sink size and air flow rate can be balanced to meet the demands of the prevailing environment. Vicor has published a series of three thermal management graphs (see datasheet) to help power system designers. The first is for a PI3101 converter without heatsink and shows a set of Ambient Temperature vs Power Output plots for various rates of forced air cooling, including natural convection. The other two show similar plots for the converter with a 6.3 mm heatsink and an 11 mm heatsink respectively.
##IMAGE_2_C##
In some applications the priority is to remove the heatsink as this will allow the closest possible proximity of adjacent PCBs. This can be done, provided the forced cooling airflow is sufficient to compensate for the absence of heatsink, with support for adequate power delivery at the known ambient temperature. For example, a converter with an 11 mm heatsink relying on natural convection cooling could deliver 32 W at 55˚C ambient. Without the heatsink, an airflow of 400 linear feet per minute (LFM) is required to ensure the same power at the same ambient temperature. A suitable compromise could be to use a 6.3 mm heatsink, where a forced air flow of 200 LFM would support converter output power to over 44 W at 55˚C ambient.
In other applications the objective is to reduce or eliminate forced air cooling, either to limit acoustic noise or to remove the reliability issues associated with fans. At 55˚C ambient, a converter with 11 mm heatsink can supply nearly 32 W max; this increases to 49 W if an airflow of 200 LFM can be tolerated, and 60 W at 400 LFM. Many other applications will have a mix of priorities driving their choice of heatsink vs forced air cooling. The plots on Vicor’s three thermal management graphs can assist designers in finding the best balance for their particular environment.
By Robert Gendron, Vice President, Marketing & Business Development, Vicor
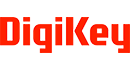